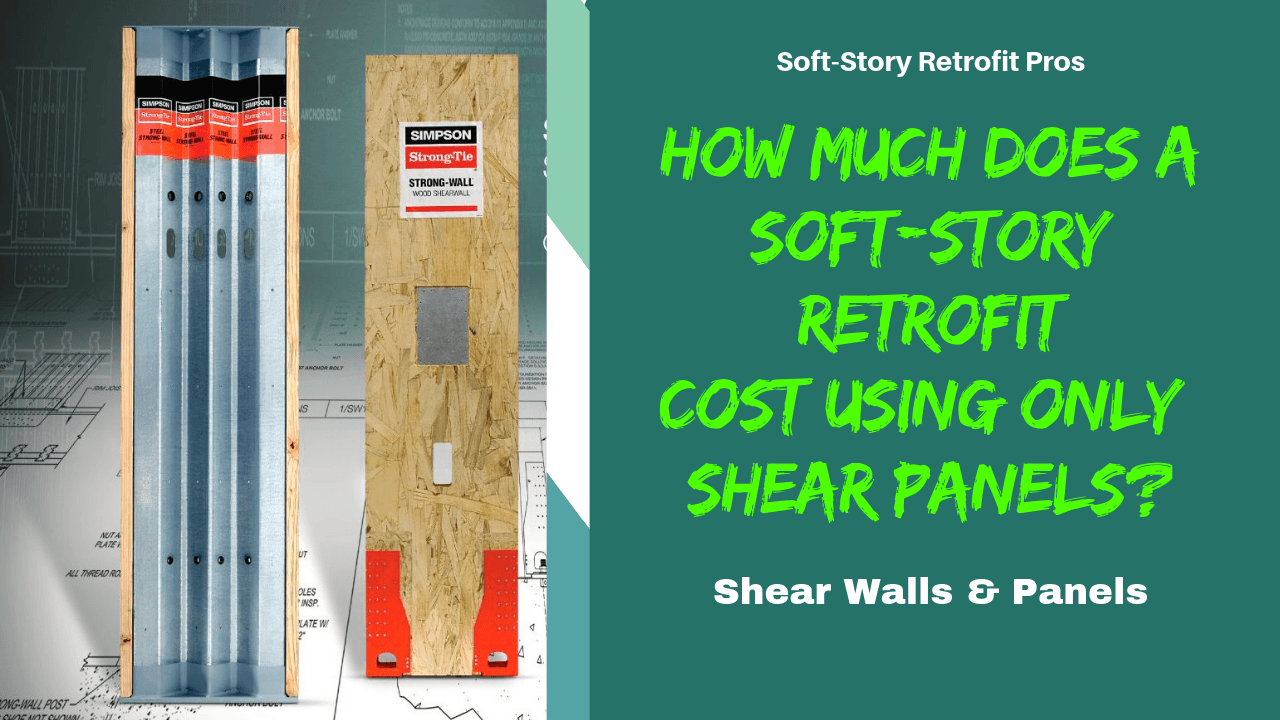
Shear Panels are the most affordable solution. But are they right for you?
How Much Does a Small Soft-Story Retrofit Cost Using Only Shear Walls?
The soft-story retrofit programs of Los Angeles and Santa Monica are well underway, and by now several property owners have already finished their retrofit projects. Luckily for those that own smaller buildings, a small soft-story retrofit repair can cost as little as $18,000 to $25,000.
Small apartment buildings with small openings will only require the installation of plywood shear walls or steel shear panels. In this small article, we will cover the cost of a soft-story retrofit repair that only utilizes shear walls as the solution. We will briefly cover the different types of shear walls available, and what you can expect to pay for engineering plans that use a shear wall solution.
Shear Wall Solution
In our hypothetical scenario, our building is small, so it only requires minimal reinforcement. Shear panels are a good solution and they will help you comply with retrofit ordinances, but we should also clarify that the shear wall solution is only adequate for small buildings. Large and heavy buildings will require a stronger level of protection by using components like cantilevered beams, or moment frames, in addition to shear panels. Do not expect to pay $18,000 for a 20 -unit apartment building that has large tuck-in parking areas.
Building Profile
- Number of units: Between 4 to 6 units
- Accessibility: The areas that require reinforcement can be easily accessed by heavy equipment.
- Number of Shear Walls: A total of six shear walls (3 in the front & 3 on the sides)
- Infrastructure: The retrofit repair will not impact plumbing lines or electrical lines
- Number of Stories: Small buildings typically have a single story above the parking area.
- Topography: The lot is big and flat.
Plywood Shearwalls
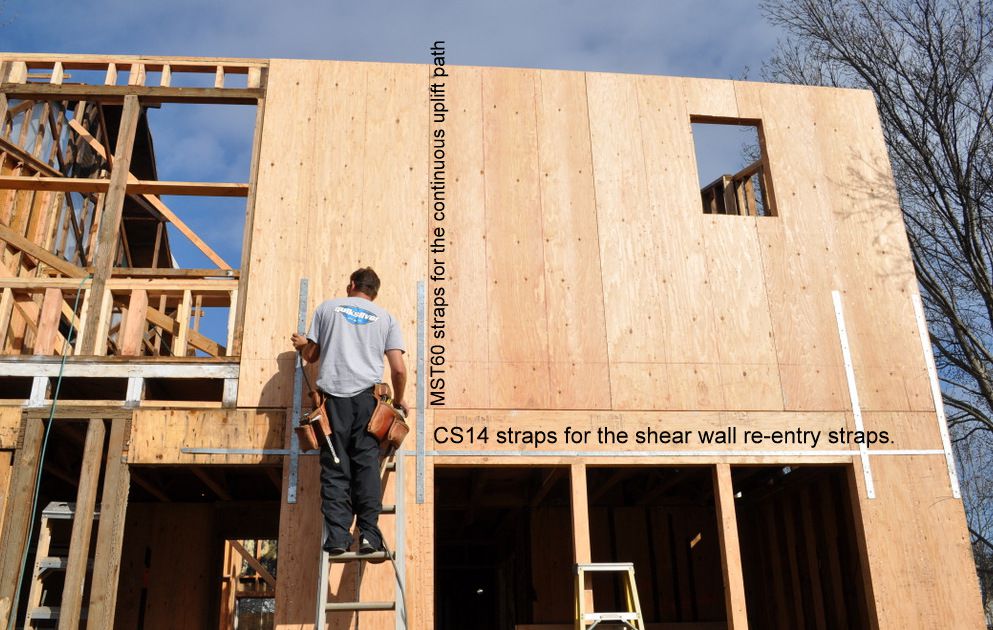
"Plywood Shear Panels in Wood-Frame Construction"
Shear walls are strengthened sections of walls that are engineering to provide additional lateral strength to a building. They are designed to resist both wind and seismic forces. Traditionally, shear walls are made of lumber, specifically plywood. Structural plywood is made of thin layers of wood chips that are all bonded together to create a stronger sheet, that’s why plywood is used to board up homes during hurricane season. You can see an example of a plywood shear wall in the picture above. It illustrates the installation for plywood panels on a wood-frame two story home. They are made on site from special Structural -1 plywood sheets. On a soft-story retrofit, the shear wall is anchored to the foundation using special “hold-down” hardware. These walls undergo a high degree of scrutiny by building officials because of the importance to the structural integrity of the building. You can see an example of the hold-down connections below.
Bolt Down Connections
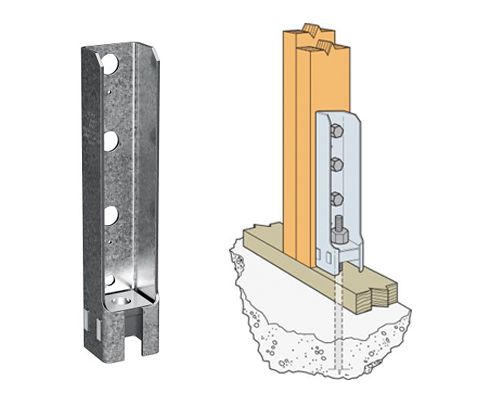
"Simpson Strong-Tie HD Connection"
But in the last decade, newer structural products have entered the market; steel shear panels, made by manufacturers like Simpson Strong-Tie and Mitek USA. Simpson Strong-Tie manufactures the “Strong-Wall” and MiTek manufactures the “HFX Hardi Frame”. These two companies dominate the steel shear wall market. Engineers love these products because the manufacturer has spent millions of dollars on Research and Development, and they offer complete sets of engineering drawings and calculations that structural engineers can use to develop their own plans. Shear panels are a great option for when space is an issue, a single shear panel can give you the same shear equivalent of a 6-foot plywood panel. Bellow, you can see an example of a Simpson Strong-Wall, available in both Plywood and Steel versions.
Simpson Strong-Wall
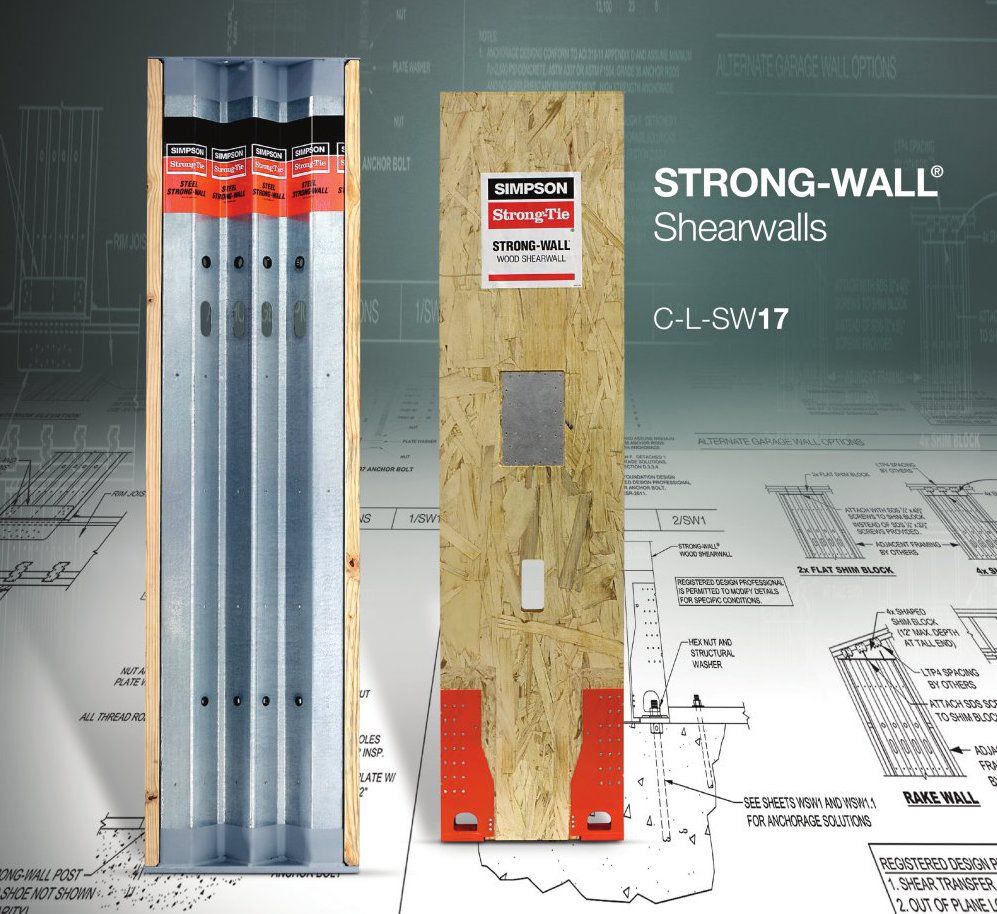
"Strong-Wall Shearwalls used in Retrofit Construction"
Shear Panel Engineering Plans
For a small soft-story building you can expect to pay anywhere from $5,500 to $7,500 for a set of engineering plans. Using shear walls as a retrofit solution does not require extensive engineering, so you’d be paying less for engineering plans when using a shear panel solution.
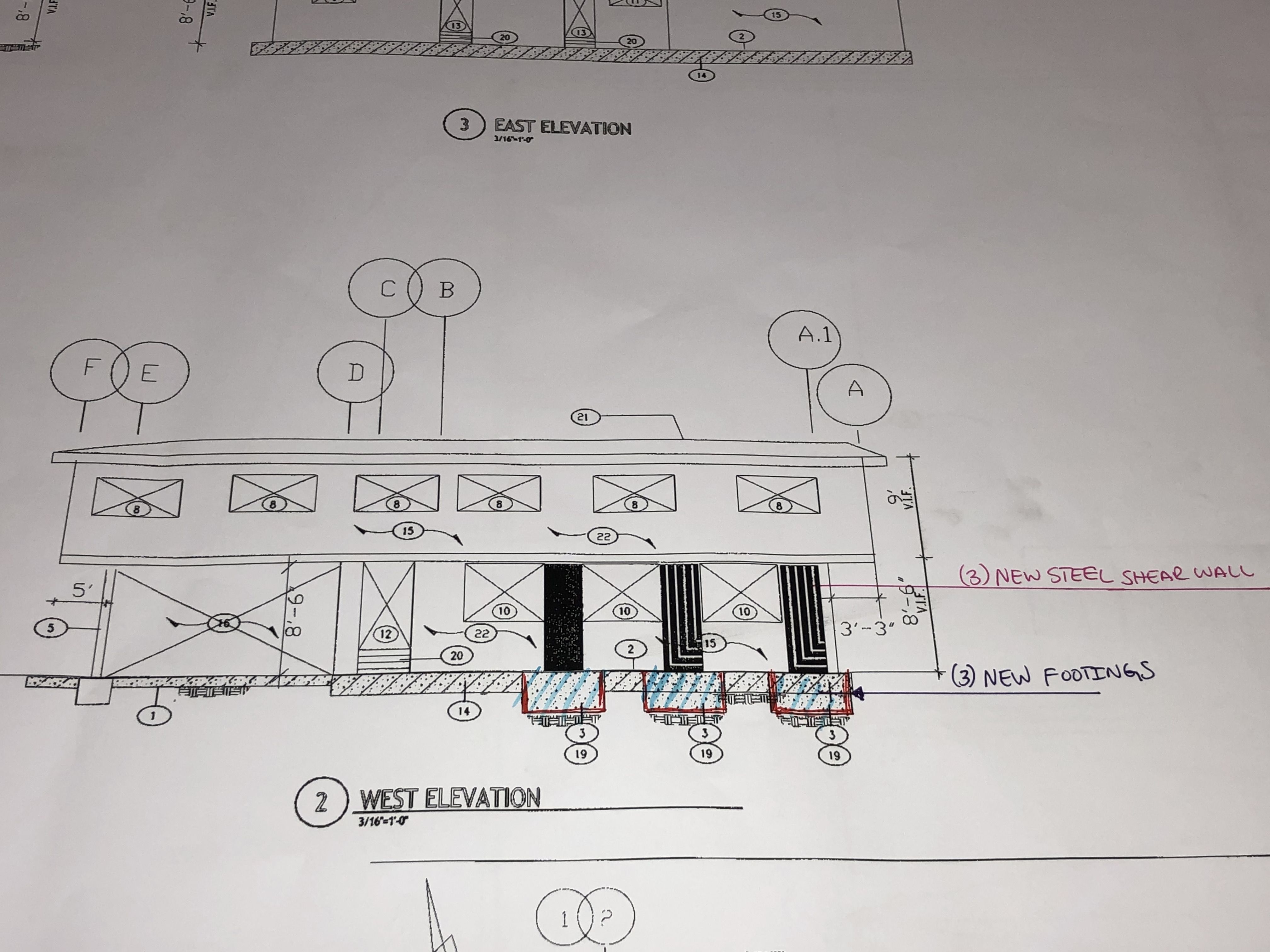
"Shear Panels drawing in Engineering Plans"
What are the major cost factors?
- Framing - connecting the new shear-wall panels to the existing beam is not a major cost factor but the full line of blocking above the beam can be a time-consuming component of the framing. Typically, a metal shear wall is the least expensive method used in common practice to retrofit a soft story building.
- Concrete- The concrete grade beam is a cost factor of labor and materials. It takes about a week of creating the steel stirrups and assembly of the “cage.” The concrete material is purchased and delivered by a ready-mix truck. It also has to be tested for the proper PSI strength. Most plans call for a Deputy Inspector be present to make sure that the concrete is being properly vibrated to remove air bubbles from the mix.
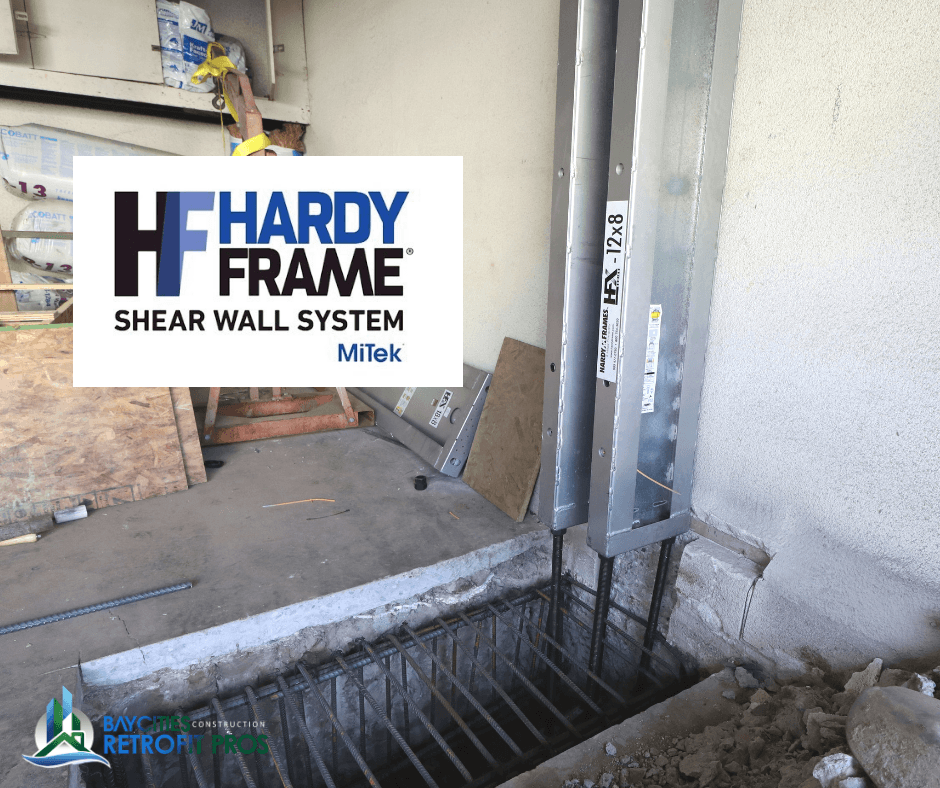
"HFX Panels used at our Santa Monica Retrofit Project"
Special conditions on this project:
- Relocation of plumbing line did add to the cost of the project.
- Saved money because the HFX panel was within the footprint of the garage. No damage to the exterior wall was required and the client saved the cost of stucco repair.
In the example we presented today, the total cost of construction for a soft-story retrofit utilizing only shear walls and shear panels as a solution comes will cost $24,483
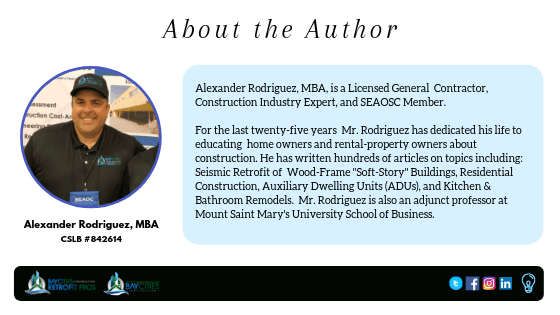